For years the American manufacturing industry has suffered from labor shortages, and during the pandemic, the labor market has become even tighter. In fact, despite lockdown restrictions easing, there are still around 515,000 jobs that need filling for the manufacturing sector to break even on its employment levels before COVID-19.
Despite the thousands of jobs on offer, reports show that companies are struggling to fill both higher-paying and entry-level positions. Why’s this the case? In short, the manufacturing sector is suffering from a drastic skills gap and has done for some time. The roots of this dilemma are somewhat complex, with some experts saying causes stem as far back as the 2008 economic recession.
That said, there are lots of misconceptions concerning the reality of manufacturing. Traditionally, when we hear the word ‘manufacturing,’ we conjure ideas of dirty and laborious manual labor. In some instances, yes, there may be a grain of truth to that. However, when we take a close look at manufacturing today, these stereotypes do the sector a considerable discredit. The industry isn’t attracting the types of technical and skilled specialists it so desperately needs to thrive.
The pervasiveness of computer-controlled machinery means that the average manufacturing worker now needs:
- Maths skills
- Intuition
- Stamina
- A high-tech skillset
… Or at least they need to be prepared to learn and finetune these skills to do their jobs justice. At the risk of sounding too reductive, the advancement in tech has significantly affected the increasing skills gap facing the manufacturing workforce.
What can manufacturing employers do to bridge the way? Although experience matters, candidates often don’t have much – if any – relevant experience when it comes to entry-level positions. So, given the current climate, it’s more important than ever to assess candidates based on their skills and potential rather than on their resume alone.
So let’s look at the top skills to search for when hiring manufacturing workers and how to assess candidate suitability.
What’s in?
Skills to look for when hiring manufacturing workers
Of course, the skills you need to identify and assess candidates for will differ somewhat depending on the role you’re looking to fill. For instance, if you’re looking to hire an order picker, attention to detail will be a priority. In contrast, for truck drivers, their necessary certifications will be more critical.
That said, if you’re unsure where to begin when it comes to which skills to assess prospective manufacturing workers for, below are some suggestions:
- Critical thinking, logic, problem solving
- Multi-tasking, ability to work under pressure
- Personal flexibility, communication, cooperation
- Initiative, pro-activity, reliability
- Attention to detail, accurate, organized work
- Disciplined, structured, precise
- Operating computers and machinery
…these are just a few examples, but you get the idea.
Below we’ll go into more detail about why some of these skills are an absolute must for workers in the manufacturing sector.
Critical thinking
Today’s manufacturing worker often has to firefight minor issues as they develop to avoid them escalating into something more significant. Often, supervisors and managers don’t have time to handle and respond to every little problem that comes along. This is why manufacturing companies look for employees who can make good decisions in the face of unexpected obstacles.
Excellent communication skills
First-rate communication skills go hand in hand with critical thinking and problem-solving. Manufacturing workers often have to work in teams to troubleshoot issues, which, of course, makes excellent communication skills a must for getting things done quickly and effectively.
Attention to detail
Manufacturing demands speed and precision, making focus and attention to detail imperative. This is especially important for workers with jobs that carry a degree of risk. For instance, a forklift driver who cannot pay close attention for extended periods of time may put the safety of you and your co-workers in jeopardy.
Dependability
Manufacturing workplaces are often vast and busy places, meaning employees have to be accountable for their productivity with little oversight. This means dependability, punctuality, and honesty are definite musts in prospective candidates.
An interest for tech
Tech is constantly evolving – and technology in the manufacturing sector is no exception. Think drones, machine learning, and artificial intelligence – these are some of the latest tech trends in manufacturing. Of course, manufacturing workers don’t need to be experts in these topics, but demonstrating a passion and a desire to learn about tech and its evolution is a real asset.
Like what you see?
Don’t miss out. Subscribe to our quarterly digest to get the latest TA and TM resources delivered right to your inbox.
How to assess for these manufacturing skills
The above list of skills may seem overwhelming. So, it stands to reason that identifying candidates with proven track records of all these traits (especially for entry-level roles) is a tall order. This is why assessing applicants’ potential is imperative.
The easiest, most accurate way of doing that is pre-employment testing. In short, these assessments are excellent for distinguishing applicants with limited industry experience but still boast the necessary skills, personality traits, and ability to learn quickly to excel in the role.
There are several ways to assess candidates for the above-mentioned skills. Below we’ve listed some of the testing methods that are most likely to predict success on the job. Let’s dive in!
Situational judgment tests (SJT)
If you’re hiring high volumes of employees for low complexity roles, then situational judgment tests are well worth considering.
As the name suggests, during an SJT, candidates are asked a series of situation-based questions explicitly relevant to the role. Typically speaking, Harver’s SJT’s only take candidates between 8-12 minutes to complete, making them a quick and engaging assessment method.
Let’s take a look at an example to get a feel for how you might apply an SJT in your manufacturing recruitment process. Suppose you’re looking to hire someone for your outbound logistics team. In that case, you might show the candidate a video scenario where they have to check the paperwork to ensure the numbers scanned correspond with what your system says.
After the candidate finishes watching this short clip, they’re given three possible ways to handle the situation and rank them from most to least effective.
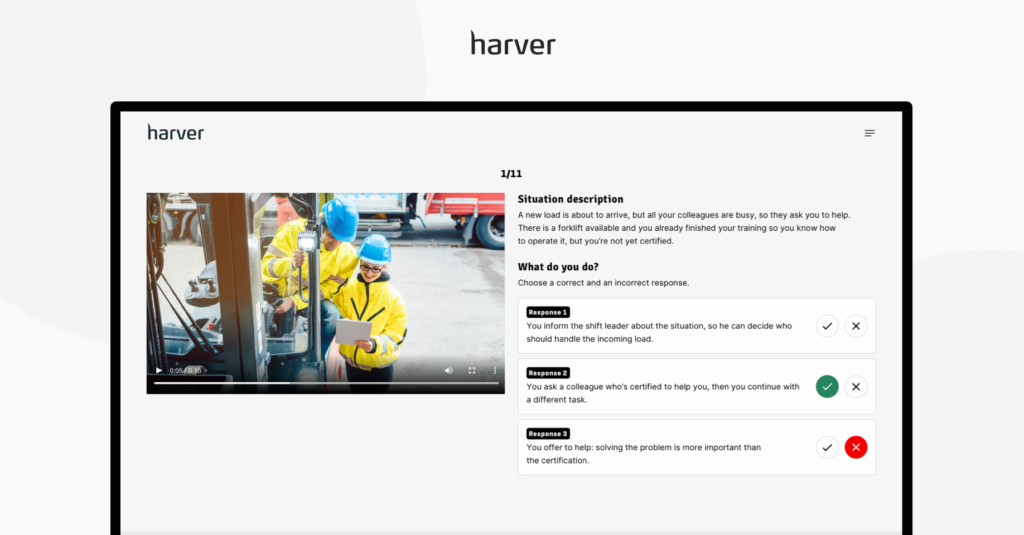
At the end of the situation judgment test, the applicant is given a score, which you can compare to employer-specific benchmarks. This goes a long way to providing an unbiased and empirical method of assessing candidate competency.
Not only that, but SJTs also equip candidates with a clearer understanding of what their day-to-day job might look like. At this point, if the applicant doesn’t think the role is for them, they can filter themselves out of the process. Although the thought of losing applicants at this stage might seem frustrating, in the long run, you’re more likely to hire loyal and committed employees.
After all, as many as 60% of new recruits who quit do so because of false expectations surrounding the role. Not only does replacing new hires disrupt day-to-day operations, but it’s expensive!
It costs roughly a third of a worker’s annual salary to recruit and train a new employee. In the long term, you’ll save lots of time and money by ensuring candidates know exactly what they’re walking into when they accept the job offer, and an SJT provides a quick and easy way of achieving exactly that.
It’s also worth noting, you can use SJT’s to evaluate a vast range of skills. From multi-tasking to critical thinking to handling stressful situations – and lots in between, you’ll undoubtedly be able to create an SJT suitable for your hiring needs. This is especially true if you opt for a custom solution rather than an out-of-the-box SJT.
If you’d like to see Harver’s SJTs in practice, or would like to learn how such assessments can be integrated into your recruitment process, you can book a demo below.
If you’d like to see how Haver can transform your hiring process,
book a demo here!
Personality questionnaire
You can also use personality tests to see whether an applicant is a good fit for your open roles and workplace culture. These tests bring the candidate’s principal personality traits to the forefront so that you can get a feel for whether their nature aligns with your company values and ethos.
This is how it works.
You, as the employer, tell us, Harver, the traits and characteristics that candidates need to possess for an excellent cultural fit. With that info to hand, we design questions that determine whether candidates boast these attributes.
At Harver, we have a People Science team who adopt a scientific approach to developing pre-employment assessments to examine a candidate’s:
- Communication skills
- Teamwork skills
- Stress resistance and the capacity to work under pressure
- Social skills
- Customer service skills
- Focus and motivation
- Response to leadership
… to name just a few.
You can learn more about Harver’s personality questionnaire below.
Skill tests
Like the other pre-employment assessments listed above, skills tests also generate an unbiased evaluation of the candidate’s ability to handle the jobs and responsibilities associated with the role. This enables manufacturing firms an inkling as to whether the candidates are skilled enough for the position they’re applying for.
Here are a few examples of the kinds of skills tests you could use to assess candidates in the manufacturing industry.
- Mechanical aptitude: This kind of skills test requires the candidate to apply technical concepts within a realistic environment to surmise the applicant’s industry know-how and problem-solving capabilities.
- Numerical reasoning: More and more manufacturing jobs demand basic maths skills. As such, setting a numerical literacy test to assess the candidate’s ability to handle units, dimensions, numerical sequences, ratios, percentages, and blueprint, and graphical interpretations.
- Attention to detail: You can use this sort of test to assess the candidate’s ability to undertake quality control procedures and adhere to production and shipping schedules. Similarly, this kind of test can also examine the applicant’s capacity to comply with your workplace’s health and safety regulations.
Next steps
Having read this article, we hope you now have a better idea of how to recruit for your vacant manufacturing positions. To get a feel for how we at Harver can help, you can book a demo of our pre-employment assessment solution below.
Ready to transform your hiring process?